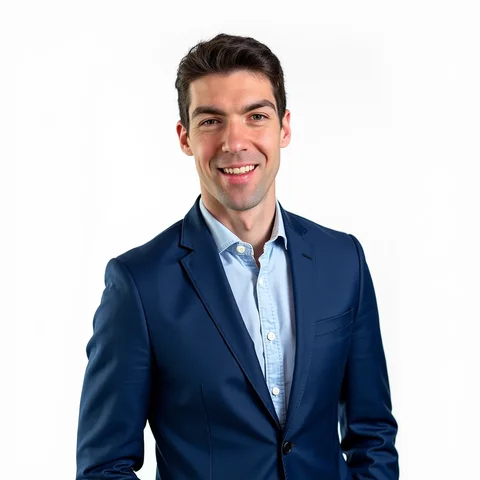
Your Photo
Alexander Poss
Experienced Software Engineer specializing in distributed systems, automation, and HMI, with a strong background in Qt, C++, Python and open-source development.
Technical Expertise
Programming Languages
- Qt/QML
- C++
- C
- Python
Systems and Design
- GUI & HMI
- Distributed Systems & Middleware
- Embedded Systems & Linux
- Model Centric SW & Code Generation
Additional Skills
- Robotics & Automation
- CAD & 3D Printing
- Electronic Engineering
- Training & Consulting